Molded case parts, a cornerstone of modern manufacturing, have revolutionized the production of numerous industrial components. These precision-crafted parts, formed through a molding process, offer a range of advantages that make them indispensable in various industries. This article explores the essence of molded case parts, their manufacturing processes, and their diverse applications across different sectors.
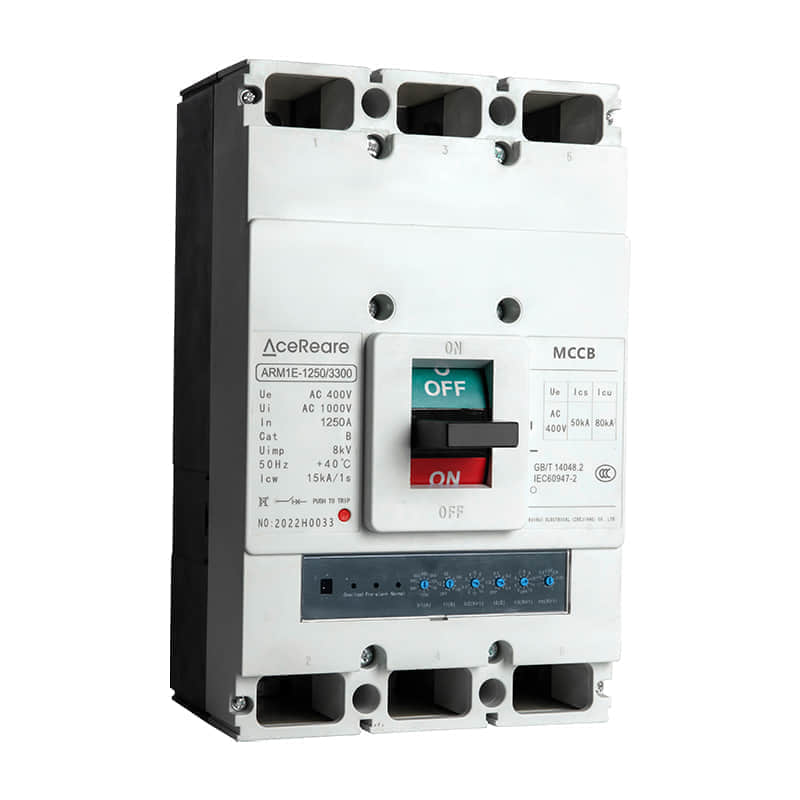
At the heart of molded case parts lies the concept of precision molding. This technique involves the use of a mold, a hollowed-out form made from materials like metal or plastic, to shape and solidify raw materials into desired shapes. The raw materials, typically thermoplastics, elastomers, or metals, are heated to a molten state and then forced into the mold cavity. Once cooled and solidified, the part is ejected from the mold, ready for further processing or assembly.
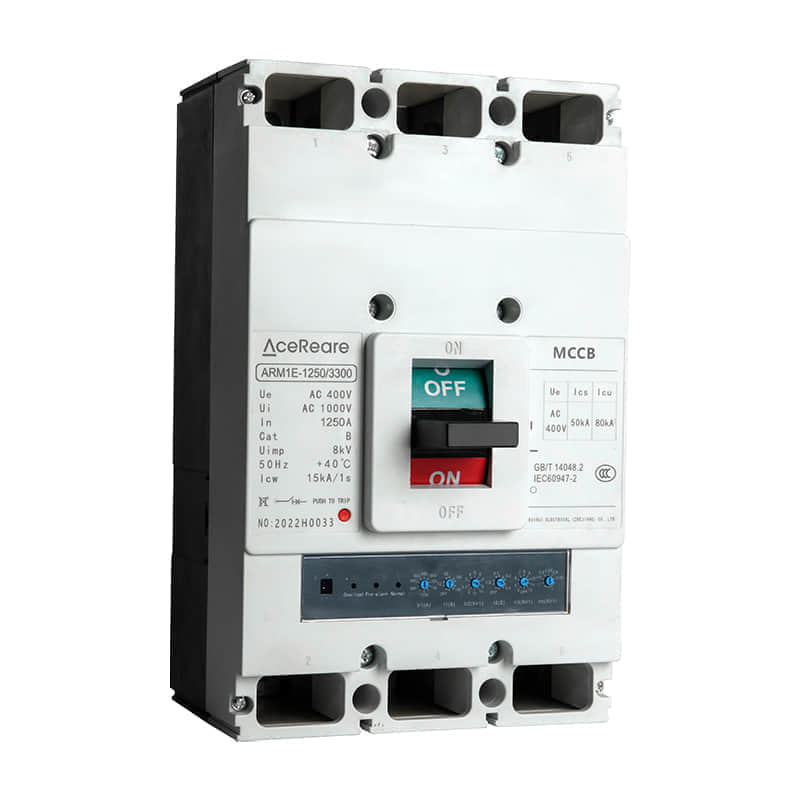
The beauty of molded case parts lies in their versatility and adaptability. Whether it’s a complex electrical connector or a simple enclosure for a mechanical device, molded case parts can be tailored to meet specific design requirements. The precision of the mold ensures that each part is identical to the original design, ensuring consistency and reliability in mass production. Moreover, molded case parts offer significant advantages over traditional manufacturing methods. For instance, they can be produced at a much faster rate, greatly improving production efficiency. Additionally, the molding process allows for the creation of intricate shapes and features that would be difficult or impossible to achieve through other methods.
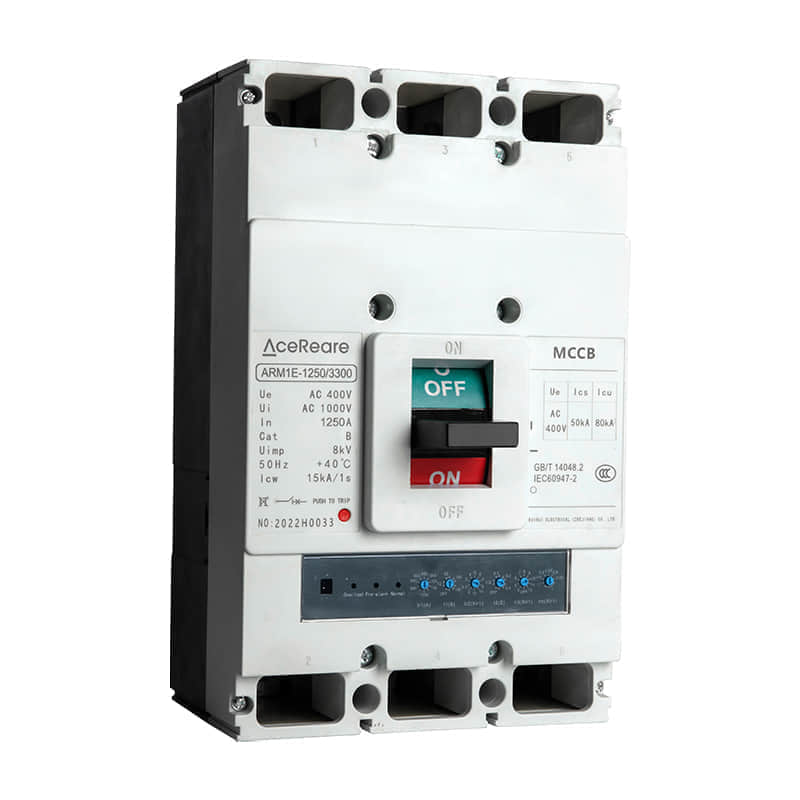
Leave a Reply